From Order to Driveway: How Auto Touch Up Paint Gets From the TouchUpDirect Factory to Your Car
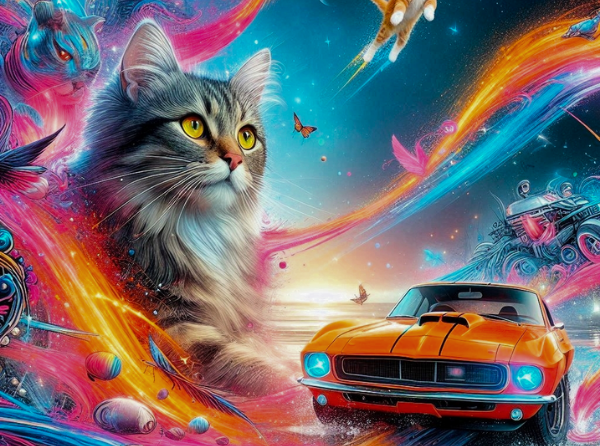
Today, we thought we’d give you a little walkthrough on how your touch up paint tool goes from an online order to a package at your front door. From the TouchUpDirect factory in Southern California, our dedicated and talented staff works hard to make sure the customer gets the paint they need for their vehicle, be it car, motorcycle, or truck. So how do our Pens, Brushes, Combos, and Aerosols get made? How do we get you the exact right paint? Join us as we take you behind the scenes to show you everything that goes into getting you your perfect color match.
The Batching Office – Touch Up Paint: The Origin
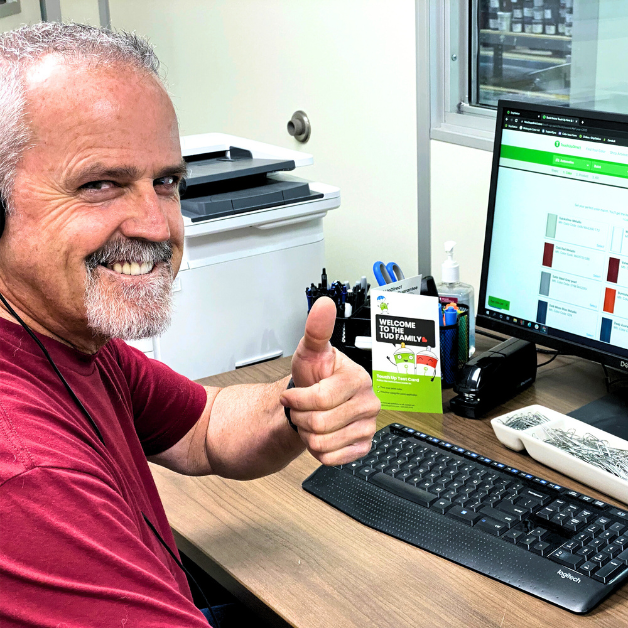
Your order first arrives in the batching office. This is where our dedicated team batches together the order before it goes out to production. What does that mean? Well this is where they put together all the necessary information people on the factory floor will need to create your order. What kind of applicator is required? Are there accessories that need to be collected for this order?
And most importantly, what color code is required to create the paint? The office then prints out a color label that travels through this entire process before being placed on your applicator.
This is also where we process returns. We have a Color Match Guarantee for the rare occasions when the customer ends up with the incorrect shade. If you get in contact with our customer service, they will work to get you one replacement color so you can get the perfect color match. It’s here in the batching office that they confirm that the replacement can be sent.
The Dashboard – The Order Log Awaits
The order information is then sent to the Dashboard, where we track pending and shipped orders. One of our employees then takes the order and heads to the paint shelves. Sometimes, we’ll get lucky and the paint will already be mixed. If that’s the case, your order goes straight to the filling station. If not, they’ll gather the elements needed to create your paint and take them to the mixing station.
The Mixing Station – Color Code Madness
The first thing to do when you’re mixing paint at the mixing station is to enter the color code. Once it has the code, the mixer can then find the exact formula you will need to mix your paint. We have access to 27,000 color codes when we’re mixing. No matter the make or model, it is likely that we have the code. Some of these colors actually stem from wildly different shades and it’s exciting to see them transform into something new!
The Filling Station – A Series of Tubes and Touch Up Paint
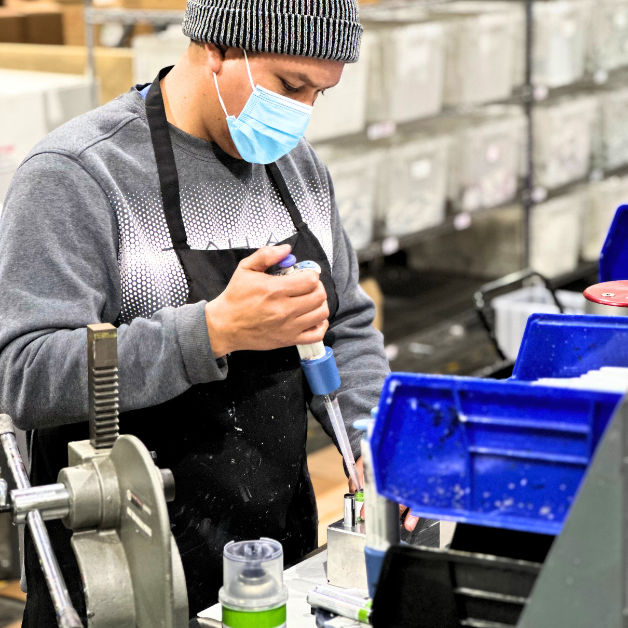
Now it’s time for your touch up paint to meet their applicator! For the Brush, it’s as easy as pouring the paint into the applicator and sealing the top on. For the Pen, the tube is filled with touch up paint and then the Pen mechanisms and cap are added. For our Aerosol Spray Paint, it’s slightly more complicated. We start with the cap. The cap is placed into the filling machine. Touch up paint is then added to the Aerosol can.
The Aerosol can is then inserted into the filling machine and the cap is pushed to the top along with the touch up paint. Once the Aerosol container is filled, you will be able to see the color inside of the clear cap. It’s part of our Aerosol filling system but it also has the added bonus of allowing the customer to see the color they’ve gotten. This is also where we apply the color label created in the batching office.
The Packing Station – Do You Need Sandpaper? We Have Lots.
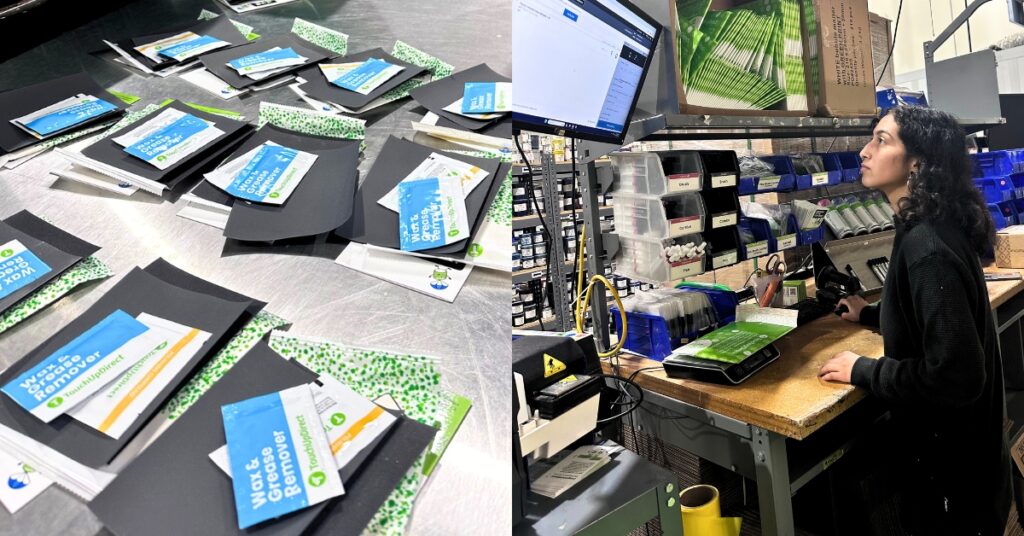
After it hits the filling station, your order will continue on to the packing station. Here, your touch up paint will be gathered up with the rest of your order and boxed. The packer scans the barcode and learns which items are needed for the order. We have an accessories station set up here so our packers can easily grab and include the required product. Accessories at the packing station include test cards, wax & grease wipes, and sandpaper. Once everything is gathered, the package is weighed and a shipping label is printed out and applied. We do one last final quality control check to make sure that everything is in place and seal it up. And there you have it. Your package is then ready to go, just chilling out in our factory until the carrier arrives to pick it up.
You’ve got scratches you need to fix up and TouchUpDirect is here to help. Choose from our wide variety of applicators, accessories, and touch up paint. We’ve got every product you’ll ever need to keep your vehicle in pristine condition. Need some help with the touch up process? We’re here to help you get the best possible coat for your car, truck, or motorcycle. Between our blog posts and the giant library of instructions we’ve created, we’ve got touch up paint walkthroughs for everyone. And if you don’t want to read, check out the many instructional videos on ourYouTube page.